Мистецтво зварювання
Мистецтво зварювання є професіоналізм, який вимагає пристрасті, інновації, якість, талант, і перш за все відданість і турботу про точність деталей.
Весь світ зварений: від найдрібніших мініатюрних аксесуарів до величезних хмарочосів, трансатлантичних кораблів, газопроводів. Ніщо з того, що є частиною нашого сьогоднішнього життя, крихітне або гігантське, не може бути виготовлено, використано, збережено або захищене без застосування процесу зварювання, тобто без цього так званого "технологічного дива", що дозволяє двом або більше металів нерозривно з'єднуватися між собою , об'єднуючи в єдину ціле сталь, алюміній, мідь, бронзу, титан, металеві сплави, оцинковані поверхні.
Сварка застосовується скрізь, де потрібно гарантувати високі експлуатаційні характеристики, навіть в найбільш екстремальних умовах навколишнього середовища і використання.
Там, де безпека виходить на перший план, як, наприклад, при виробництві транспортних засобів, від велосипеда до танка, від автомобіля до надшвидкісного потягу.
Там, де міцність повинна бути бездоганною, в області промислового і побутового будівництва, при створенні наших осель, наших робочих місць, нашого середовища проживання.
Там, де умови навколишнього середовища є екстремальними, при постійній корозії, де не можна допустити перемогу вогню і льоду, наприклад, у великих промислових установках з вилучення, виробництва, транспортування і розподілу енергії, від сонячної до атомної, в хімічній промисловості, у важкій промисловості, на плавильних установках.
Сварка також є помічником, здатним адаптуватися до наших найпростішим, але не менше від цього важливим потребам, - наприклад в області «зроби сам» - а також пристосуватися до усіх вимог при виробництві обладнання і техобслуговування в будь-яких побутових і професійних секторах.
Там, де є зварювання, присутній Telwin, пропонуючи гаму продукції, яка не має собі рівних у продажу. Технологічні, функціональні, надійні рішення, сертифіковане якість, що гарантується найбільш відомими міжнародними сертифікують організаціями даної галузі.
Весь світ зварений: від найдрібніших мініатюрних аксесуарів до величезних хмарочосів, трансатлантичних кораблів, газопроводів. Ніщо з того, що є частиною нашого сьогоднішнього життя, крихітне або гігантське, не може бути виготовлено, використано, збережено або захищене без застосування процесу зварювання, тобто без цього так званого "технологічного дива", що дозволяє двом або більше металів нерозривно з'єднуватися між собою , об'єднуючи в єдину ціле сталь, алюміній, мідь, бронзу, титан, металеві сплави, оцинковані поверхні.
Сварка застосовується скрізь, де потрібно гарантувати високі експлуатаційні характеристики, навіть в найбільш екстремальних умовах навколишнього середовища і використання.
Там, де безпека виходить на перший план, як, наприклад, при виробництві транспортних засобів, від велосипеда до танка, від автомобіля до надшвидкісного потягу.
Там, де міцність повинна бути бездоганною, в області промислового і побутового будівництва, при створенні наших осель, наших робочих місць, нашого середовища проживання.
Там, де умови навколишнього середовища є екстремальними, при постійній корозії, де не можна допустити перемогу вогню і льоду, наприклад, у великих промислових установках з вилучення, виробництва, транспортування і розподілу енергії, від сонячної до атомної, в хімічній промисловості, у важкій промисловості, на плавильних установках.
Сварка також є помічником, здатним адаптуватися до наших найпростішим, але не менше від цього важливим потребам, - наприклад в області «зроби сам» - а також пристосуватися до усіх вимог при виробництві обладнання і техобслуговування в будь-яких побутових і професійних секторах.
Там, де є зварювання, присутній Telwin, пропонуючи гаму продукції, яка не має собі рівних у продажу. Технологічні, функціональні, надійні рішення, сертифіковане якість, що гарантується найбільш відомими міжнародними сертифікують організаціями даної галузі.



Тема уроку :
Наплавлення простих і середньої складності деталей, вузлів та конструкій.
Тема уроку:
Наплавлення простих і середньої складності деталей, вузлів та конструкцій з різноманітних сплавів.
1. Зварювання сталей
2. Зварювання чавуну
3. Зварювання кольорових металів
4. Наплавлення швидкоспрацьовуваних поверхонь
1. Зварювання сталей
Сталі, які містять вуглецю до 0,27%, добре зварюються всіма способами. Сталі з підвищеним вмістом вуглецю в більшості випадків зварюються з попереднім підігрівом, а іноді з наступною термічною обробкою -- нормалізацією або відпалюванням.
Сталі, що містять легуючих елементів в сумі до 5%, належать до низьколегованих. За призначенням вони поділяються на три групи: низьколеговані маловуглецеві, низьколеговані середиьовуглецеві і низьколеговані жароміцні.
Низьколеговані маловуглецеві сталі містять вуглецю до 0,22%. їх легують хромом, марганцем, кремнієм, нікелем, міддю, титаном і використовують як будівні сталі в суднобудуванні, транспортному машинобудуванні і т. д.
До низьколегованих середньовуглецевих відносяться сталі, які містять вуглецю від 0,20 до 0,40%. Найбільш широко використовують хромокремнемарганцеві сталі марок 20ХГС, 25ХГСА, ЗОХГСА, що мають підвищену міцність і пружність.
До низьколегованих жароміцних належать сталі, які легуються в основному хромом, молібденом, ванадієм і вольфрамом. Використовують їх при виготовленні пароенергетичних установок, які працюють при температурах до 500° С і більше.
Низьколеговані сталі зварюють різними способами. Однак, на відміну від звичайних маловуглецевих сталей, вони, подібно до сталей з підвищеним вмістом вуглецю, мають підвищений нахил до загартування і утворення загартувальних тріщин в зоні термічного впливу.
Тому більшість низьколегованих сталей при товщині понад 10 мм зварюють з попереднім підігрівом до температури від 150 до 350° С, а після зварювання піддають термічній обробці -- нормалізації чи високотемпературному відпусканню.
Для виготовлення електродів, що застосовуються для зварювання цих сталей, використовують низьколегований зварювальний дріт. Електродні покриття, як правило, мають фтористо-кальцієву шлакову основу.
Хромисті нержавіючі сталі з вмістом хрому від 12 до 18% при наявності вуглецю вище 0,1 % мають різко виражений нахил до загартування на повітрі. Тому зварювання цих сталей, щоб уникнути появлення в зварюваних швах і в навколошовних зонах структури мартенситу, виконують з обов'язковим підігрівом до 200--250° С і наступним відпалом або високотемпературним відпусканням. У практиці широко застосовують дугове зварювання хромистих сталей електродами з хромонікелевого дроту або дроту того ж складу, що й основний метал, з покриттям типу УОНІ-13.
Хромисті сталі, які містять хрому більше 25%, наприклад марок Х25, Х28, належать до феритного класу. Вони мають високу кислотостійкість і окалиностійкість при нагріванні до температури 1000-- 1100° і є незагартовними.
При зварюванні феритних хромистих сталей в металі шва утворюється крупнозерниста структура з низькими механічними властивостями. В навколошовній зоні також відбувається інтенсивний ріст зерна, що властиве однофазним сталям, які не зазнають фазових змін з зміною температури.
Структура і механічні властивості швів на цих сталях трохи поліпшуються, якщо в електродні покриття ввести титан, алюміній і інші елементи, які сприяють здрібненню зерна. Застосовують також проковування зварних швів. Сталі марок Х25 і Х28 зварюють електродами, металевий стержень яких має такий самий склад, що й основний метал.
Хромонікелеві аустенітні сталі мають високу корозійну стійкість і широко використовуються для виготовлення хімічної і нафтової апаратури, особливо сталь марки Х18Н9, що має 18--20% хрому і 8--11% нікелю. Ці сталі зварюються всіма способами і значно краще хромистих.
Основними труднощами при зварюванні хромонікелевих сталей є утворення при температурах 500--700° С карбідів хрому і випадання їх по границях зерен, що значно погіршує антикорозійні властивості зварних з'єднань. Щоб перешкодити цьому явищу, зварювання хромонікелевих сталей ведуть при мінімальному розігріві і великих швидкостях охолодження. Для повного відновлення аустенітної структури після зварювання рекомендується вироби піддавати загартуванню від температур 1050--1100° С з наступним швидким охолодженням У воді.
Ручне дугове зварювання виконують на малих струмах аустенітними хромонікелевими електродами малого діаметра, що мають покриття типу УОНІ-13.
Газове зварювання здійснюють з застосуванням флюсів з бури, борної кислоти і плавикового шпату, а при автоматичному дуговому і електрошлаковому зварюванні використовують спеціальні марки флюсів.
Зварювальний дріт у всіх випадках застосовують того ж складу, що й основний метал, але з більш низьким вмістом вуглецю і з присадками титану, молібдену, ніобію і інших елементів.
Тонколистові вироби успішно зварюють на точкових і шовних контактних машинах, в середовищі вуглекислого газу, аргонодуговим способом.
2. Зварювання чавуну
Зварювання чавуну застосовується при виправленні браку в чавунних виливках, при ремонтних роботах, наприклад при зварюванні тріщин у блоках циліндрів двигунів, в станинах верстатів і пресів, а також при виготовленні зварно-литих конструкцій з високоміцних чавунів.
Чавун, як відомо, містить більшу кількість вуглецю (3,5--4%), кремнію (0,5--4,5%), сірки (до 0,2%) і фосфору (до 2,0%), ніж сталь, що сильно утруднює його зварювання.
При швидкому остиганні розтопленого чавуну утворюється відбілений чавун, який має велику твердість і крихкість. Високий вміст таких домішок, як сірка і фосфор, ще сильніше знижує пластичність чавуну і збільшує його здатність до утворення тріщин.
Тому основними труднощами при зварюванні чавуну є появлення зон відбілювання і утворення тріщин як у наплавленому, так і в основному металі. Щоб цього уникнути, зварювання чавуну слід вести з попереднім підігрівом і з наступним уповільненим охолодженням. Однак такий метод зварювання дуже трудомісткий і не завжди може бути використаний. Тому в практиці застосовуються три основних способи зварювання чавуну: гарячий, напівгарячий і холодний.
При гарячому зварюванні цьому способі всю деталь перед зварюванням нагрівають у горнах, печах або спеціальних тимчасових нагрівальних пристроях, опалюваних деревним вугіллям або коксом, до температури 500--600° С.
Дефектні місця перед зварюванням вирубують зубилом до здорового металу. Розробку кромок провадять під кутом 90°. Щоб розплавлюваний метал не витікав при наскрізному проплавленні або не розтікався по поверхні виробів, місця зварювання формують графітовими або вугільними пластинками. Щілини між пластинками і виробами забивають формовим піском, замішаним на рідкому склі. Як присаднийметал застосовують чавунні стержні діаметром від 5 до 15 мм, які містять від 3 до 3,5% вуглецю і від 3 до 4,6% кремнію.
Гаряче зварювання чавуну найчастіше виконують ацетиленово-кисневим нормальним або з невеликим надлишком ацетилену полум'ям. Як флюс використовують прожарену буру або суміш бури (50%) і соди (50%).
Після зварювання деталь повільно охолоджують разом з піччю; для цього її засипають сухим піском або шлаком. Гаряче зварювання чавуну забезпечує найкращу якість зварних з'єднань без зон відбілювання і тріщин. Наплавлений метал після зварювання легко піддається механічній обробці. Проте, будучи складним і досить трудомістким процесом, гаряче зварювання чавуну застосовується головним чином для найбільш відповідальних деталей або деталей, що мають складну форму (блоки циліндрів, станини деяких пресів та Ін.).
При напівгарячому зварюванні провадиться тільки часткове нагрівання деталі (переважно в місцях зварювання) до температури 250--450° С. Такий метод застосовується при зварюванні деталей невеликої товщини і при невеликому об'ємі наплавленого металу. Зварювання ведеться ацетиленово-кисневим полум'ям і рідше -- електродуговим способом вугільними електродами.
Зварені деталі, так само як і при гарячому способі, для повільного остигання засипають сухим піском або шлаком.
При холодному зварюванні. чавунні деталі зварюють за методом Слов'янова без підігріву. Існують такі його різновидності.
Зварювання електродами із маловуглецевої сталі. Його застосовують при ремонті невідповідальних деталей, а також деталей, які після зварювання не потребують механічної обробки. Маловідповідальні деталі зварюють електродами з крейдяним покриттям.
Ремонт більш складних і більш відповідальних деталей (станин і рам потужних дизелів, циліндрів газоповітродувних машин, станин верстатів, корпусів електродвигунів великої потужності та ін.) провадять електродами з якісними покриттями, наприклад типу УОНІ-13, і з постановкою на різьбі по кромках деталей стальних шпильок.
Зварювання електродами із монель-металу. Монель-метал являє собою мідно-нікелевий сплав, що містить близько 70% нікелю і близько 30% міді. Зварювання монель-металом в більшості випадків застосовують тоді, коли потрібно одержати м'який метал шва, що легко піддається механічній обробці. До недоліків цього способу слід віднести недостатню механічну міцність зварного з'єднання і високу вартість електродів.
Зварювання мідними і .мідно-залізними електродами. При зварюванні такими електродами, як і електродами із .монель-металу, забезпечується невелике нагрівання основного металу і утворення незначної зони відбілювання. Це дає можливість провадити механічну обробку порівняно в'язкого і не дуже твердого металу шва. Мідно-залізні електроди виготовляють електролітичним нанесенням міді на залізні стержні або обгортанням мідних стержнів смужкою з чорної або білої жерсті. На електроди наносять крейдяне покриття. Застосовують такожпучки електродів, що складаються з одного чи двох стальних електродів з якісним покриттям і одного мідного стержня.
Зварювання залізо-нікелевими електродами. При зварюванні залі-зо-нікелевими електродами у шві утворюється сплав заліза з нікелем, що має до 50% нікелю. Такі електроди використовують при холодному зварюванні складних виливків з високоміцного чавуну, що вимагає після зварювання механічної обробки.
3. Зварювання кольорових металів
Мідь відрізняється від сталі тим, що має високу теплопровідність, яка майже в 6 раз перевищує теплопровідність сталі, інтенсивно поглинає і розчиняє різні гази, утворюючи з киснем закис Си20 і окис СиО міді. Закис міді з міддю створює евтектику, температура плавлення якої (1064° С) нижче температури плавлення міді (1083° С). При затвердненні рідкої міді ця евтектика розташовується по границях зерен, робить мідь крихкою і схильною до утворення тріщин. Тому основним завданням при зварюванні міді є захист її від окислення і активне розкислення зварювальної ванни.
Найбільш поширене газове зварювання міді ацетиленово-кисневим полум'ям за допомогою пальників в 1,5--2 рази потужніших, ніж при зварюванні сталей. Присадним металом служать мідні прутки, що містять як розкислювачі до 0,25% фосфору і до 1,25% кремнію, а також фосфориста бронза, до складу якої входить 0,25% фосфору і 1,5--10% олова.
При товщині виробів більше 5--6 мм їх попередньо підігрівають до температури 250--300° С. Флюсами при зварюванні служать прожарена бура або суміш, що складається з 70% бури і 30% борної кислоти.
Для підвищення механічних властивостей і поліпшення структури наплавленого металу мідь після зварювання проковують при температурі близько 200--300° С. Проковану мідь знову нагрівають до 500-- 550° С і охолоджують у воді.
Мідь можна зварювати також електродуговим способом вугільними або металевими електродами, в струмені захисних газів під шаром флюсу на конденсаторних машинах, способом тертя.
Латунь, так само як і мідь, в більшості випадків зварюють ацетиленово-кисневим полум'ям. Газове зварювання латуні ведуть окислювальним полум'ям, при якому на поверхні ванни з'являється плівка тугоплавкого окису цинку, що зменшує дальше вигоряння і випаровування цинку. Як присадний метал застосовують латунний дріт з присадкою до 0,5% кремнію. Флюси використовують ті ж самі, що і при зварюванні міді.
При нагріванні бронзи вище температури 500° С вона втрачає в'язкість і стає крихкою. Для запобігання з'явленню тріщин під час зварювання застосовують попередній підігрів до 300--450° С.
Всі сорти бронзи мають цілком задовільну зварюваність. Бронзи, що містять олово, найчастіше зварюють ацетилено-кисневим полум'ямз застосуванням тих же флюсів, що й при зварюванні міді. Присадним металом служить фосфориста бронза або латунь. Алюмінієві або алюмінієво-залізисті бронзи краще зварюються електродуговим способом вугільними або металевими електродами. Як присадний метал в цьому випадку застосовують прутки такого ж складу, що й основний метал, а як флюси або електродні покриття -- хлористі і фтористі сполуки калію і натрію.
Основними факторами, що утруднюють зварювання алюмінію, є низька температура його плавлення (658° С), велика теплопровідність (яка приблизно в три рази перевищує теплопровідність сталі), утворення тугоплавких окислів алюмінію А1203, що мають температуру плавлення 2050° С і щільність (3,9 * 103 кГ/м3), яка значно перевищує щільність алюмінію (2,7 * 103 кГІм8). Крім того, ці окисли слабо реагують як з кислими, так і з основними флюсами і тому погано видаляються із шва.
Найбільш широко використовують газове зварювання алюмінію ацетиленово-кисневим полум'ям. За останні роки значного поширення набуло також автоматичне дугове зварювання металевими електродами під флюсом і в середовищі аргону. При всіх способах зварювання, за винятком аргонодугового, застосовують флюси або покриті електроди, до складу яких входять хлористі і фтористі сполуки літію, калію, натрію і інших елементів. Під впливом флюсів А1203 переходить в летючий АІСІд, що має низьку щільність (2,4 * 103 кГ/м3) і самосубліма-ційний при температурі 183 С. Як присадний метал при всіх способах зварювання використовують дріт або стержні того ж складу, що й основний метал.
До сплавів алюмінію, які широко застосовуються в техніці, належать алюмінієво-марганцевисті, алюмінієво-магнієві, алюмінієво-мідні і алюмінієво-кремнисті. Перші два сплави мають хорошу зварюваність і їх зварюють аналогічно алюмінію. Гірше зварюються два інших сплави --дуралюміній і силумін, які звичайно зварюють ацетиленово-кисневим полум'ям.
Із магнієвих сплавів для зварних конструкцій використовують переважно магнієво-марганцевисті, які краще інших зварюються за допомогою контактного, газового і аргонодугового зварювання. При газовому зварюванні обов'язково застосовують фторидні флюси, які на відміну від хлоридних не викликають корозії зварних з'єднань. Дугове зварювання магнієвих сплавів металевими електродами через низьку якість зварних швів до цього часу не застосовується.
При зварюванні магнієвих сплавів спостерігається великий ріст зерна у навколошовних ділянках і сильний розвиток стовпчастих кристалів у зварному шві. Тому границя міцності зварних з'єднань становить 55--60% границі міцності основного металу.
Нікель і деякі його сплави зварюють вольфрамовим електродом в аргоні, дуговим зварюванням покритими електродами і під флюсом. Зварювання в аргоні виконують на постійному струмі при прямій полярності. При ручному, як і при автоматичномузварюванні під флюсом, як присадний метал використовують дріт того ж складу, що й основний метал. На електродні стержні наносять покриття типу УОНІ-13/45; автоматичне зварювання здійснюється під фторидними флюсами.
Титан зварюють вольфрамовими електродами в середовищі інертних газів і плавкими металевими електродами під фторидними і хлоридними флюсами, які не містять кисневих сполук. Зварювання в середовищі інертних газів ведуть на постійному струмі прямої полярності, а зварювання під флюсом -- на постійному струмі зворотної полярності.
Газове зварювання для титану і його сплавів не застосовується.
Свинець зварюють ацетиленово-кисневим і воднево-кисневим полум'ям. Зварювання виконують в нижньому положенні з застосуванням присадного металу або без нього.
При виготовленні конструкцій з цирконію, танталу і ніобію найбільш поширене зварювання в аргоні і гелії вольфрамовими і плавкими електродами, а також електронним променем у вакуумі.
Молібден зварюють як електронним променем у вакуумі, так і вольфрамовими електродами в камерах з контрольованою атмосферою. Як контрольовану атмосферу використовують захисні інертні гази -- аргон або гелій, якими заповнюються вакуумні камери.
5. Наплавлення швидкоспрацьовуваних поверхонь
Тверді наплавки застосовують при виготовленні нових і відновленні спрацьованих деталей, які піддаються швидкому спрацьовуванню. Для їх одержання використовують тверді сплави, порошкові або зерноподібні суміші, спеціальні наплавні електроди, порошкові дроти або стрічки, чавунну суцільну стрічку і легуючі флюси.
До литих твердих сплавів належать пруткові сплави, що виготовляються на вольфрамохромокобальтовій основі типу ВКЗ, а також на хромо-залізонікелевій основі типу сормайт. Цими сплавами провадиться наплавлення за способом Слов'янова або ацетиленово-кисневим полум'ям деталей машин, які працюють на стирання, штампів для гарячого і холодного штампування, ущільнюючих поверхонь пароводяної арматури, що працює при високих параметрах пари і т. д. Твердість (НRС 40-- 60) наплавок досягається за рахунок введення вольфраму, хрому, вуглецю, марганцю і інших елементів, що входять до складу цих сплавів. До порошкових або зернистих сумішей належать сталініт і вокар. Сталініт являє собою суміш, що складається з ферохрому, феромарганцю, чавунної стружки і нафтового коксу. До складу вокару входить вуглець, кремній, вольфрам і залізо. Більш широке застосування має сталініт, яким за допомогою вугільної дуги наплавляють зуби екска-ваторів, ножі бульдозерів, щоки каменедробарок та ін. При наплавленні сталінітом твердість наплавок досягає НRС 60 і вище.
Для одержання наплавок, що мають твердість НRС 25--67, у промисловості застосовують значне число різних марок електродів. Так, наприклад, для наплавлення залізничних рейкових кінців і хрестовин та автотракторних деталей, середня твердість яких повинна бутиНRС 25--40, використовують електроди, якими легують метал наплавок хромом і марганцем або одним марганцем, що міститься в електродному покритті. При наплавленні деталей дробильно-розмельного устаткування, землерийних і буді-вельношляхових машин застосовують електроди, які забезпечують одержання наплавок високої твердості (НRС 58--64). Це досягається за рахунок хрому, вуглецю і бору, що переходять у наплавлений метал з електродних покриттів.
При виготовленні наплавленого різального інструменту з матеріалу типу швидкорізальної сталі Р18, який має твердість близько HRС 62--67, наплавлений метал легують вольфрамом, хромом, ванадієм і іншими елементами, що входять в електродні стержні чи електродні покриття.
При виготовленні зубців ковшів екскаваторів, траків гусеничних тракторів, щок каменедробарок і інших деталей, які швидко спрцьовуються, досить часто використовують високомарганцевисту литу сталь, що містить 11--16% марганцю і 0,8--1,4% вуглецю. Вироби з цієї сталі після сильного спрацьовування піддаються відновлюваль-ному наплавленню електродуговим способом. У більшості випадків застосовують наплавлення ручним способом за допомогою електродів, які забезпечують одержання високомарганцевистих або хромонікелевих аустенітних наплавок невисокої твердості (порядку НВ 180-- 280), але великої в'язкості і високої зносостійкості. Для одержання аустенітної структури метал наплавок при яскраво-червоному гартуванні рекомендується охолоджувати водою або струменем стисненого повітря.
При автоматичному дуговому наплавленні під флюсом для одержання твердих наплавок різного складу і властивостей застосовують порошкові дроти і стрічки, легуючі флюси, чавунну стрічку. Порошкові дроти і стрічки виготовляють порожнистими на спеціальних протяжних верстатах із стальних стрічок холодного прокату. Для цієї мети використовують стрічки товщиною від 0,2 до 1 мм і шириною від 8 до 100 мм. В порожнинну частину дроту і стрічки в процесі їх виготовлення запресовують порошкову легуючу шихту, яка складається із суміші різних феросплавів і вуглецю.
Автоматичне наплавлення під флюсом широко застосовують для наплавки валів прокатних станів, великого різального інструменту, штампів холодного і гарячого штампування і т. д.
Тема уроку :
Тема уроку:
Наплавлення простих і середньої складності деталей, вузлів та конструкцій з різноманітних сплавів.
1. Зварювання сталей
2. Зварювання чавуну
3. Зварювання кольорових металів
4. Наплавлення швидкоспрацьовуваних поверхонь
1. Зварювання сталей
Сталі, які містять вуглецю до 0,27%, добре зварюються всіма способами. Сталі з підвищеним вмістом вуглецю в більшості випадків зварюються з попереднім підігрівом, а іноді з наступною термічною обробкою -- нормалізацією або відпалюванням.
Сталі, що містять легуючих елементів в сумі до 5%, належать до низьколегованих. За призначенням вони поділяються на три групи: низьколеговані маловуглецеві, низьколеговані середиьовуглецеві і низьколеговані жароміцні.
Низьколеговані маловуглецеві сталі містять вуглецю до 0,22%. їх легують хромом, марганцем, кремнієм, нікелем, міддю, титаном і використовують як будівні сталі в суднобудуванні, транспортному машинобудуванні і т. д.
До низьколегованих середньовуглецевих відносяться сталі, які містять вуглецю від 0,20 до 0,40%. Найбільш широко використовують хромокремнемарганцеві сталі марок 20ХГС, 25ХГСА, ЗОХГСА, що мають підвищену міцність і пружність.
До низьколегованих жароміцних належать сталі, які легуються в основному хромом, молібденом, ванадієм і вольфрамом. Використовують їх при виготовленні пароенергетичних установок, які працюють при температурах до 500° С і більше.
Низьколеговані сталі зварюють різними способами. Однак, на відміну від звичайних маловуглецевих сталей, вони, подібно до сталей з підвищеним вмістом вуглецю, мають підвищений нахил до загартування і утворення загартувальних тріщин в зоні термічного впливу.
Тому більшість низьколегованих сталей при товщині понад 10 мм зварюють з попереднім підігрівом до температури від 150 до 350° С, а після зварювання піддають термічній обробці -- нормалізації чи високотемпературному відпусканню.
Для виготовлення електродів, що застосовуються для зварювання цих сталей, використовують низьколегований зварювальний дріт. Електродні покриття, як правило, мають фтористо-кальцієву шлакову основу.
Хромисті нержавіючі сталі з вмістом хрому від 12 до 18% при наявності вуглецю вище 0,1 % мають різко виражений нахил до загартування на повітрі. Тому зварювання цих сталей, щоб уникнути появлення в зварюваних швах і в навколошовних зонах структури мартенситу, виконують з обов'язковим підігрівом до 200--250° С і наступним відпалом або високотемпературним відпусканням. У практиці широко застосовують дугове зварювання хромистих сталей електродами з хромонікелевого дроту або дроту того ж складу, що й основний метал, з покриттям типу УОНІ-13.
Хромисті сталі, які містять хрому більше 25%, наприклад марок Х25, Х28, належать до феритного класу. Вони мають високу кислотостійкість і окалиностійкість при нагріванні до температури 1000-- 1100° і є незагартовними.
При зварюванні феритних хромистих сталей в металі шва утворюється крупнозерниста структура з низькими механічними властивостями. В навколошовній зоні також відбувається інтенсивний ріст зерна, що властиве однофазним сталям, які не зазнають фазових змін з зміною температури.
Структура і механічні властивості швів на цих сталях трохи поліпшуються, якщо в електродні покриття ввести титан, алюміній і інші елементи, які сприяють здрібненню зерна. Застосовують також проковування зварних швів. Сталі марок Х25 і Х28 зварюють електродами, металевий стержень яких має такий самий склад, що й основний метал.
Хромонікелеві аустенітні сталі мають високу корозійну стійкість і широко використовуються для виготовлення хімічної і нафтової апаратури, особливо сталь марки Х18Н9, що має 18--20% хрому і 8--11% нікелю. Ці сталі зварюються всіма способами і значно краще хромистих.
Основними труднощами при зварюванні хромонікелевих сталей є утворення при температурах 500--700° С карбідів хрому і випадання їх по границях зерен, що значно погіршує антикорозійні властивості зварних з'єднань. Щоб перешкодити цьому явищу, зварювання хромонікелевих сталей ведуть при мінімальному розігріві і великих швидкостях охолодження. Для повного відновлення аустенітної структури після зварювання рекомендується вироби піддавати загартуванню від температур 1050--1100° С з наступним швидким охолодженням У воді.
Ручне дугове зварювання виконують на малих струмах аустенітними хромонікелевими електродами малого діаметра, що мають покриття типу УОНІ-13.
Газове зварювання здійснюють з застосуванням флюсів з бури, борної кислоти і плавикового шпату, а при автоматичному дуговому і електрошлаковому зварюванні використовують спеціальні марки флюсів.
Зварювальний дріт у всіх випадках застосовують того ж складу, що й основний метал, але з більш низьким вмістом вуглецю і з присадками титану, молібдену, ніобію і інших елементів.
Тонколистові вироби успішно зварюють на точкових і шовних контактних машинах, в середовищі вуглекислого газу, аргонодуговим способом.
2. Зварювання чавуну
Зварювання чавуну застосовується при виправленні браку в чавунних виливках, при ремонтних роботах, наприклад при зварюванні тріщин у блоках циліндрів двигунів, в станинах верстатів і пресів, а також при виготовленні зварно-литих конструкцій з високоміцних чавунів.
Чавун, як відомо, містить більшу кількість вуглецю (3,5--4%), кремнію (0,5--4,5%), сірки (до 0,2%) і фосфору (до 2,0%), ніж сталь, що сильно утруднює його зварювання.
При швидкому остиганні розтопленого чавуну утворюється відбілений чавун, який має велику твердість і крихкість. Високий вміст таких домішок, як сірка і фосфор, ще сильніше знижує пластичність чавуну і збільшує його здатність до утворення тріщин.
Тому основними труднощами при зварюванні чавуну є появлення зон відбілювання і утворення тріщин як у наплавленому, так і в основному металі. Щоб цього уникнути, зварювання чавуну слід вести з попереднім підігрівом і з наступним уповільненим охолодженням. Однак такий метод зварювання дуже трудомісткий і не завжди може бути використаний. Тому в практиці застосовуються три основних способи зварювання чавуну: гарячий, напівгарячий і холодний.
При гарячому зварюванні цьому способі всю деталь перед зварюванням нагрівають у горнах, печах або спеціальних тимчасових нагрівальних пристроях, опалюваних деревним вугіллям або коксом, до температури 500--600° С.
Дефектні місця перед зварюванням вирубують зубилом до здорового металу. Розробку кромок провадять під кутом 90°. Щоб розплавлюваний метал не витікав при наскрізному проплавленні або не розтікався по поверхні виробів, місця зварювання формують графітовими або вугільними пластинками. Щілини між пластинками і виробами забивають формовим піском, замішаним на рідкому склі. Як присаднийметал застосовують чавунні стержні діаметром від 5 до 15 мм, які містять від 3 до 3,5% вуглецю і від 3 до 4,6% кремнію.
Гаряче зварювання чавуну найчастіше виконують ацетиленово-кисневим нормальним або з невеликим надлишком ацетилену полум'ям. Як флюс використовують прожарену буру або суміш бури (50%) і соди (50%).
Після зварювання деталь повільно охолоджують разом з піччю; для цього її засипають сухим піском або шлаком. Гаряче зварювання чавуну забезпечує найкращу якість зварних з'єднань без зон відбілювання і тріщин. Наплавлений метал після зварювання легко піддається механічній обробці. Проте, будучи складним і досить трудомістким процесом, гаряче зварювання чавуну застосовується головним чином для найбільш відповідальних деталей або деталей, що мають складну форму (блоки циліндрів, станини деяких пресів та Ін.).
При напівгарячому зварюванні провадиться тільки часткове нагрівання деталі (переважно в місцях зварювання) до температури 250--450° С. Такий метод застосовується при зварюванні деталей невеликої товщини і при невеликому об'ємі наплавленого металу. Зварювання ведеться ацетиленово-кисневим полум'ям і рідше -- електродуговим способом вугільними електродами.
Зварені деталі, так само як і при гарячому способі, для повільного остигання засипають сухим піском або шлаком.
При холодному зварюванні. чавунні деталі зварюють за методом Слов'янова без підігріву. Існують такі його різновидності.
Зварювання електродами із маловуглецевої сталі. Його застосовують при ремонті невідповідальних деталей, а також деталей, які після зварювання не потребують механічної обробки. Маловідповідальні деталі зварюють електродами з крейдяним покриттям.
Ремонт більш складних і більш відповідальних деталей (станин і рам потужних дизелів, циліндрів газоповітродувних машин, станин верстатів, корпусів електродвигунів великої потужності та ін.) провадять електродами з якісними покриттями, наприклад типу УОНІ-13, і з постановкою на різьбі по кромках деталей стальних шпильок.
Зварювання електродами із монель-металу. Монель-метал являє собою мідно-нікелевий сплав, що містить близько 70% нікелю і близько 30% міді. Зварювання монель-металом в більшості випадків застосовують тоді, коли потрібно одержати м'який метал шва, що легко піддається механічній обробці. До недоліків цього способу слід віднести недостатню механічну міцність зварного з'єднання і високу вартість електродів.
Зварювання мідними і .мідно-залізними електродами. При зварюванні такими електродами, як і електродами із .монель-металу, забезпечується невелике нагрівання основного металу і утворення незначної зони відбілювання. Це дає можливість провадити механічну обробку порівняно в'язкого і не дуже твердого металу шва. Мідно-залізні електроди виготовляють електролітичним нанесенням міді на залізні стержні або обгортанням мідних стержнів смужкою з чорної або білої жерсті. На електроди наносять крейдяне покриття. Застосовують такожпучки електродів, що складаються з одного чи двох стальних електродів з якісним покриттям і одного мідного стержня.
Зварювання залізо-нікелевими електродами. При зварюванні залі-зо-нікелевими електродами у шві утворюється сплав заліза з нікелем, що має до 50% нікелю. Такі електроди використовують при холодному зварюванні складних виливків з високоміцного чавуну, що вимагає після зварювання механічної обробки.
3. Зварювання кольорових металів
Мідь відрізняється від сталі тим, що має високу теплопровідність, яка майже в 6 раз перевищує теплопровідність сталі, інтенсивно поглинає і розчиняє різні гази, утворюючи з киснем закис Си20 і окис СиО міді. Закис міді з міддю створює евтектику, температура плавлення якої (1064° С) нижче температури плавлення міді (1083° С). При затвердненні рідкої міді ця евтектика розташовується по границях зерен, робить мідь крихкою і схильною до утворення тріщин. Тому основним завданням при зварюванні міді є захист її від окислення і активне розкислення зварювальної ванни.
Найбільш поширене газове зварювання міді ацетиленово-кисневим полум'ям за допомогою пальників в 1,5--2 рази потужніших, ніж при зварюванні сталей. Присадним металом служать мідні прутки, що містять як розкислювачі до 0,25% фосфору і до 1,25% кремнію, а також фосфориста бронза, до складу якої входить 0,25% фосфору і 1,5--10% олова.
При товщині виробів більше 5--6 мм їх попередньо підігрівають до температури 250--300° С. Флюсами при зварюванні служать прожарена бура або суміш, що складається з 70% бури і 30% борної кислоти.
Для підвищення механічних властивостей і поліпшення структури наплавленого металу мідь після зварювання проковують при температурі близько 200--300° С. Проковану мідь знову нагрівають до 500-- 550° С і охолоджують у воді.
Мідь можна зварювати також електродуговим способом вугільними або металевими електродами, в струмені захисних газів під шаром флюсу на конденсаторних машинах, способом тертя.
Латунь, так само як і мідь, в більшості випадків зварюють ацетиленово-кисневим полум'ям. Газове зварювання латуні ведуть окислювальним полум'ям, при якому на поверхні ванни з'являється плівка тугоплавкого окису цинку, що зменшує дальше вигоряння і випаровування цинку. Як присадний метал застосовують латунний дріт з присадкою до 0,5% кремнію. Флюси використовують ті ж самі, що і при зварюванні міді.
При нагріванні бронзи вище температури 500° С вона втрачає в'язкість і стає крихкою. Для запобігання з'явленню тріщин під час зварювання застосовують попередній підігрів до 300--450° С.
Всі сорти бронзи мають цілком задовільну зварюваність. Бронзи, що містять олово, найчастіше зварюють ацетилено-кисневим полум'ямз застосуванням тих же флюсів, що й при зварюванні міді. Присадним металом служить фосфориста бронза або латунь. Алюмінієві або алюмінієво-залізисті бронзи краще зварюються електродуговим способом вугільними або металевими електродами. Як присадний метал в цьому випадку застосовують прутки такого ж складу, що й основний метал, а як флюси або електродні покриття -- хлористі і фтористі сполуки калію і натрію.
Основними факторами, що утруднюють зварювання алюмінію, є низька температура його плавлення (658° С), велика теплопровідність (яка приблизно в три рази перевищує теплопровідність сталі), утворення тугоплавких окислів алюмінію А1203, що мають температуру плавлення 2050° С і щільність (3,9 * 103 кГ/м3), яка значно перевищує щільність алюмінію (2,7 * 103 кГІм8). Крім того, ці окисли слабо реагують як з кислими, так і з основними флюсами і тому погано видаляються із шва.
Найбільш широко використовують газове зварювання алюмінію ацетиленово-кисневим полум'ям. За останні роки значного поширення набуло також автоматичне дугове зварювання металевими електродами під флюсом і в середовищі аргону. При всіх способах зварювання, за винятком аргонодугового, застосовують флюси або покриті електроди, до складу яких входять хлористі і фтористі сполуки літію, калію, натрію і інших елементів. Під впливом флюсів А1203 переходить в летючий АІСІд, що має низьку щільність (2,4 * 103 кГ/м3) і самосубліма-ційний при температурі 183 С. Як присадний метал при всіх способах зварювання використовують дріт або стержні того ж складу, що й основний метал.
До сплавів алюмінію, які широко застосовуються в техніці, належать алюмінієво-марганцевисті, алюмінієво-магнієві, алюмінієво-мідні і алюмінієво-кремнисті. Перші два сплави мають хорошу зварюваність і їх зварюють аналогічно алюмінію. Гірше зварюються два інших сплави --дуралюміній і силумін, які звичайно зварюють ацетиленово-кисневим полум'ям.
Із магнієвих сплавів для зварних конструкцій використовують переважно магнієво-марганцевисті, які краще інших зварюються за допомогою контактного, газового і аргонодугового зварювання. При газовому зварюванні обов'язково застосовують фторидні флюси, які на відміну від хлоридних не викликають корозії зварних з'єднань. Дугове зварювання магнієвих сплавів металевими електродами через низьку якість зварних швів до цього часу не застосовується.
При зварюванні магнієвих сплавів спостерігається великий ріст зерна у навколошовних ділянках і сильний розвиток стовпчастих кристалів у зварному шві. Тому границя міцності зварних з'єднань становить 55--60% границі міцності основного металу.
Нікель і деякі його сплави зварюють вольфрамовим електродом в аргоні, дуговим зварюванням покритими електродами і під флюсом. Зварювання в аргоні виконують на постійному струмі при прямій полярності. При ручному, як і при автоматичномузварюванні під флюсом, як присадний метал використовують дріт того ж складу, що й основний метал. На електродні стержні наносять покриття типу УОНІ-13/45; автоматичне зварювання здійснюється під фторидними флюсами.
Титан зварюють вольфрамовими електродами в середовищі інертних газів і плавкими металевими електродами під фторидними і хлоридними флюсами, які не містять кисневих сполук. Зварювання в середовищі інертних газів ведуть на постійному струмі прямої полярності, а зварювання під флюсом -- на постійному струмі зворотної полярності.
Газове зварювання для титану і його сплавів не застосовується.
Свинець зварюють ацетиленово-кисневим і воднево-кисневим полум'ям. Зварювання виконують в нижньому положенні з застосуванням присадного металу або без нього.
При виготовленні конструкцій з цирконію, танталу і ніобію найбільш поширене зварювання в аргоні і гелії вольфрамовими і плавкими електродами, а також електронним променем у вакуумі.
Молібден зварюють як електронним променем у вакуумі, так і вольфрамовими електродами в камерах з контрольованою атмосферою. Як контрольовану атмосферу використовують захисні інертні гази -- аргон або гелій, якими заповнюються вакуумні камери.
5. Наплавлення швидкоспрацьовуваних поверхонь
Тверді наплавки застосовують при виготовленні нових і відновленні спрацьованих деталей, які піддаються швидкому спрацьовуванню. Для їх одержання використовують тверді сплави, порошкові або зерноподібні суміші, спеціальні наплавні електроди, порошкові дроти або стрічки, чавунну суцільну стрічку і легуючі флюси.
До литих твердих сплавів належать пруткові сплави, що виготовляються на вольфрамохромокобальтовій основі типу ВКЗ, а також на хромо-залізонікелевій основі типу сормайт. Цими сплавами провадиться наплавлення за способом Слов'янова або ацетиленово-кисневим полум'ям деталей машин, які працюють на стирання, штампів для гарячого і холодного штампування, ущільнюючих поверхонь пароводяної арматури, що працює при високих параметрах пари і т. д. Твердість (НRС 40-- 60) наплавок досягається за рахунок введення вольфраму, хрому, вуглецю, марганцю і інших елементів, що входять до складу цих сплавів. До порошкових або зернистих сумішей належать сталініт і вокар. Сталініт являє собою суміш, що складається з ферохрому, феромарганцю, чавунної стружки і нафтового коксу. До складу вокару входить вуглець, кремній, вольфрам і залізо. Більш широке застосування має сталініт, яким за допомогою вугільної дуги наплавляють зуби екска-ваторів, ножі бульдозерів, щоки каменедробарок та ін. При наплавленні сталінітом твердість наплавок досягає НRС 60 і вище.
Для одержання наплавок, що мають твердість НRС 25--67, у промисловості застосовують значне число різних марок електродів. Так, наприклад, для наплавлення залізничних рейкових кінців і хрестовин та автотракторних деталей, середня твердість яких повинна бутиНRС 25--40, використовують електроди, якими легують метал наплавок хромом і марганцем або одним марганцем, що міститься в електродному покритті. При наплавленні деталей дробильно-розмельного устаткування, землерийних і буді-вельношляхових машин застосовують електроди, які забезпечують одержання наплавок високої твердості (НRС 58--64). Це досягається за рахунок хрому, вуглецю і бору, що переходять у наплавлений метал з електродних покриттів.
При виготовленні наплавленого різального інструменту з матеріалу типу швидкорізальної сталі Р18, який має твердість близько HRС 62--67, наплавлений метал легують вольфрамом, хромом, ванадієм і іншими елементами, що входять в електродні стержні чи електродні покриття.
При виготовленні зубців ковшів екскаваторів, траків гусеничних тракторів, щок каменедробарок і інших деталей, які швидко спрцьовуються, досить часто використовують високомарганцевисту литу сталь, що містить 11--16% марганцю і 0,8--1,4% вуглецю. Вироби з цієї сталі після сильного спрацьовування піддаються відновлюваль-ному наплавленню електродуговим способом. У більшості випадків застосовують наплавлення ручним способом за допомогою електродів, які забезпечують одержання високомарганцевистих або хромонікелевих аустенітних наплавок невисокої твердості (порядку НВ 180-- 280), але великої в'язкості і високої зносостійкості. Для одержання аустенітної структури метал наплавок при яскраво-червоному гартуванні рекомендується охолоджувати водою або струменем стисненого повітря.
При автоматичному дуговому наплавленні під флюсом для одержання твердих наплавок різного складу і властивостей застосовують порошкові дроти і стрічки, легуючі флюси, чавунну стрічку. Порошкові дроти і стрічки виготовляють порожнистими на спеціальних протяжних верстатах із стальних стрічок холодного прокату. Для цієї мети використовують стрічки товщиною від 0,2 до 1 мм і шириною від 8 до 100 мм. В порожнинну частину дроту і стрічки в процесі їх виготовлення запресовують порошкову легуючу шихту, яка складається із суміші різних феросплавів і вуглецю.
Автоматичне наплавлення під флюсом широко застосовують для наплавки валів прокатних станів, великого різального інструменту, штампів холодного і гарячого штампування і т. д.
Тема уроку :
ДУГОВЕ РІЗАННЯ МЕТАЛУ: СУТЬ ПРОЦЕСУ ТА ЙОГО ПЕРЕВАГИ
Дугове різання заснована на розплавлення металевої деталі в місці різу, а також подальшому її видаленні за допомогою тиску дуги і власної ваги (іноді в видаленні розплавленого металу з місця різу застосовується додатковий потік повітря).
Повітряно-дугове різання матеріалу часто виконується вручну за допомогою вугільних або покритих металевих електродів. Відносно робочого матеріалу, то дугового обробці під силу робота з чавуном, високолегованої сталі, кольоровими металами, а також сплавами.
Якість різу, як правило, низька (маються нерівні кромки, покриті оплавилася металом і шлаком). Таким чином, для подальшого застосування зварювального обладнання обов’язково потрібно механічна обробка. До того ж продуктивність повітряно-дугового обробки матеріалу невисока.
Електродугова різання не вимоглива до застосування спеціального обладнання. Різка із застосуванням дуги може застосовуватися в тих місцях, де застосовується дугове зварювання. Здійснювати процес можна в будь-якому просторовому положенні.
Універсальність процедури за допомогою дуги дозволяє працювати з вуглецевими і низьколегованими сталями. Для видалення всіляких дефектів зварного шва, виплавлення канавок в основному робочому матеріалі може застосовуватися поверхнева, а також розділова різання металу.
РОЗДІЛОВА ДУГОВЕ РІЗАННЯ
Під час розділової процедури виріб встановлюється в найбільш сприятливий для витікання металу становище. При здійсненні вертикального різу різання ведеться зверху вниз. Подібна визначеність напрямку необхідна для того, щоб розплавлений матеріал не засмічував зроблений розріз.
Для того щоб відхилити дугу магнітним дуттям в сторону різу, другий зварювальний кабель приєднується у початку різу зверху. Розділова електродугова різання починає виконуватися з середини листа або кромки. Якщо робота починається з середини листа, то спочатку прорізається отвір. Після цього, зробивши нахил електрода таким чином, щоб кратер розташовувався на торцевій крайці різу, деталь оплавляется.
У тому випадку, якщо товщина розрізає металевої деталі менше діаметра електрода, відбувається наступне: робочий елемент розташовується по відношенню до робочої поверхні перпендикулярно, після чого переміщується вздовж лінії різу.
РІЗКА ОТВОРІВ
Якщо в матеріалі потрібно вирізати великий отвір, то спочатку виконується невелике. Для вирізки маленького отвору необхідно відступити від краю різу всередину, після чого продовжити рез, поступово виводячи на краю основного отвору.
Під час роботи з металевими деталями особлива увага повинна приділятися запобіганню тіла від бризок, крапель металу, а також шлаку, оскільки вони можуть завдати істотної шкоди, викликавши опіки. Також варто пам’ятати, що від металевих надлишків може стати причиною пожежі.
ПОВЕРХНЕВА ДУГОВЕ РІЗАННЯ
Поверхнева електродугова різання передбачає нахил катода до робочої поверхні під кутом 5-20 °. Потім електрод переміщається і частково занурюється в утворену порожнину. Щодо широких канавок скажімо, що вони виконуються поперечними коливаннями електрода в положенні вертикально.
Показник глибини канавки повністю залежить від швидкості переміщення електричної дуги, а також нахилу електрода. Глибока канавка виконується за допомогою декількох проходів. Електрод встановлюється в положенні перпендикулярно по відношенню до робочої поверхні в тому випадку, якщо потрібно прорізання круглих отворів різного діаметру. При цьому порушується дуга може бути більшою довжини.
РІЗКА МЕТАЛЕВИМ ЕЛЕКТРОДОМ
Електродугова різання за допомогою металевого електрода має на увазі використання товсто покритих катодів, часто застосовуються в зварювальному справі. Рід електричного струму залежить від маркування електрода.
Швидкість розділової процедури здебільшого залежить від товщини розрізає металевої деталі, а також величини струму і діаметра катода. При збільшенні товщини металевої деталі швидкість розділового процесу значно зменшується.
Для того щоб зробити рез графітовим або вугільним катодом, застосовується дія постійного електричного струму прямої полярності, оскільки в цьому випадку виділяється більша кількість впливає на деталь тепла. Коксування кромок металу ускладнює їх подальшу механічну роботу. Варто зазначити, що ширина різу більше, ніж у випадку застосування металевого електрода.
ПЕРЕВАГИ ТА НЕДОЛІКИ ДУГОВОГО РІЗАННЯ МЕТАЛУ
Ручна дугова різання металів часто виконується металевим електродом. У більшості випадків такий спосіб застосовується в будівельно-монтажних роботах. Різання металу робиться за допомогою змінного або постійного струму, катодами різних марок і діаметрів, які застосовуються при зварюванні металевих деталей.
Разом з тим, широко поширені саме електроди для різання металу з товстим покриттям. Електрод для різання деталей захищена від замикання завдяки козирка.
Різання металу дугою може здійснюватися катодами, діаметр яких коливається в межах 3-10 міліметрів. Під час різання електричний струм приймається більшим, ніж під час зварювання металу (приблизно на 10-30%).
Основними недоліками дугового обробки металу є погана якість виконуваного різу, а також низька продуктивність. Незважаючи на деякі недоліки, сучасної будівельної і виробничої сфер просто напросто не обійтися без різання матеріалу.
Тема уроку:
Дефекти зварних з’єднань та способи їх усунення
Види дефектів.Дефекти зварних з'єднань бувають зовнішні і внутрішні. До зовнішніх дефектів при дуговому і газовому зварюванні належать: нерівномірність поперечного перерізу по довжині швів, незаплавлені кратери, підрізи основного металу, зовнішні тріщини, відкриті пори тощо. Внутрішні дефекти: непроварення кромки або несплавлення окремих шарів при багатошаровому зварюванні, внутрішні пори і тріщини, шлакові включення тощо.
Контактне точкове і шовне зварювання може дати великі вм'ятини в основному металі, які ослаблюють місця зварювання, пропалини і виплески металу, а всередині зварних з'єднань - тріщини, пори та інші дефекти.
Причини утворення дефектів.Дефекти в зварних з'єднаннях утворюються з різних причин. При дуговому і газовому зварюванні переріз швів буде нерівномірним, якщо порушено режим зварювання або низька кваліфікація зварника. Причинами підрізів здебільшого є велика сила струму і велика потужність зварювального пальника.
Основна причина утворення пор у зварних швах - насиченість їх воднем, азотом та іншими газами, що потрапляють у шов при зварюванні електродами зі зволоженим покриттям, або при наявності оксидів чи інших забруднень на кромках зварюваного металу.
Тріщини і непровари є найбільш небезпечними дефектами зварних з'єднань. Тріщини утворюються найчастіше під час зварювання сталей із підвищеним вмістом вуглецю або легувальних домішок та коли метал шва насичений сіркою, фосфором або іншими шкідливими елементами. Причинами непроварів можуть бути мала сила струму або недостатня потужність пальника, погане зачищення кромок основного металу або шарів при багатошаровому зварюванні, низька кваліфікація зварника, неправильна технологія складання і зварювання деталей.


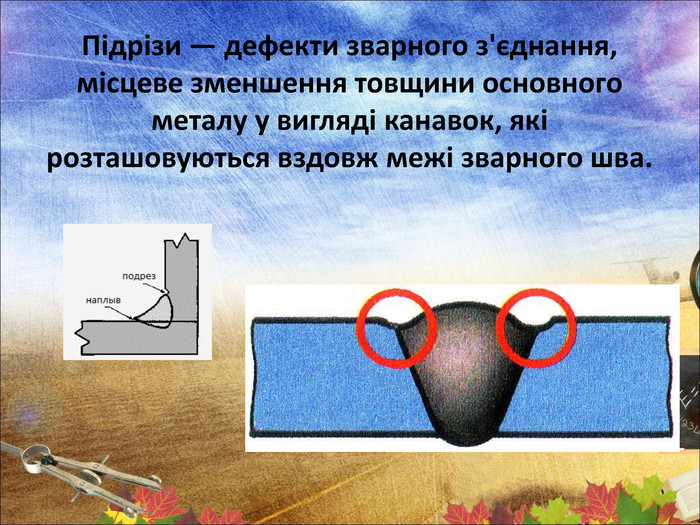





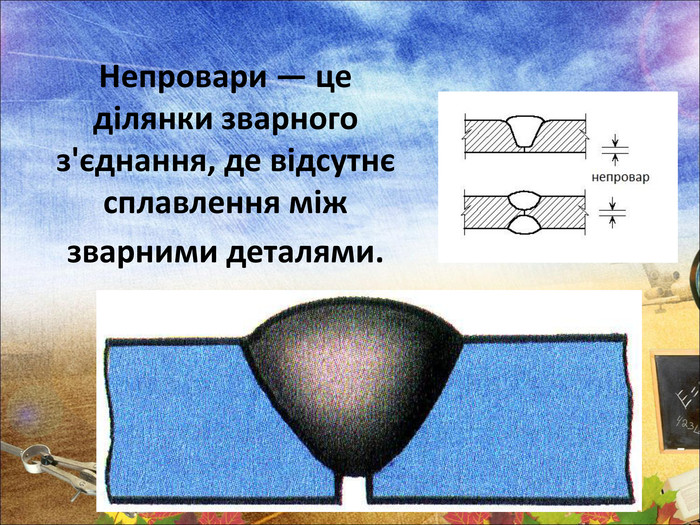





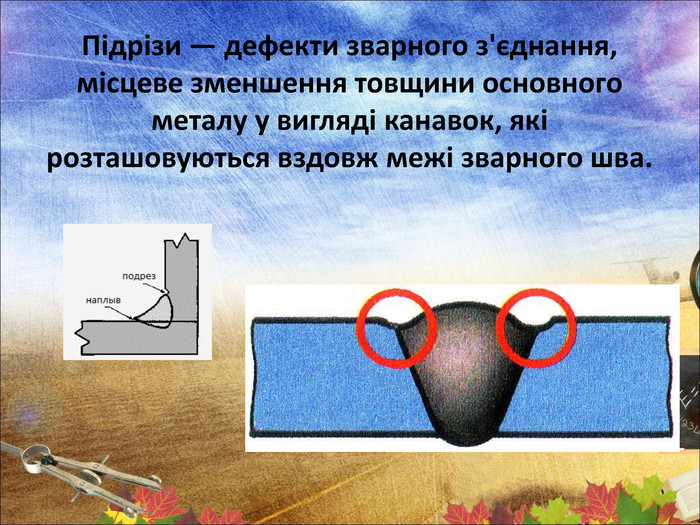





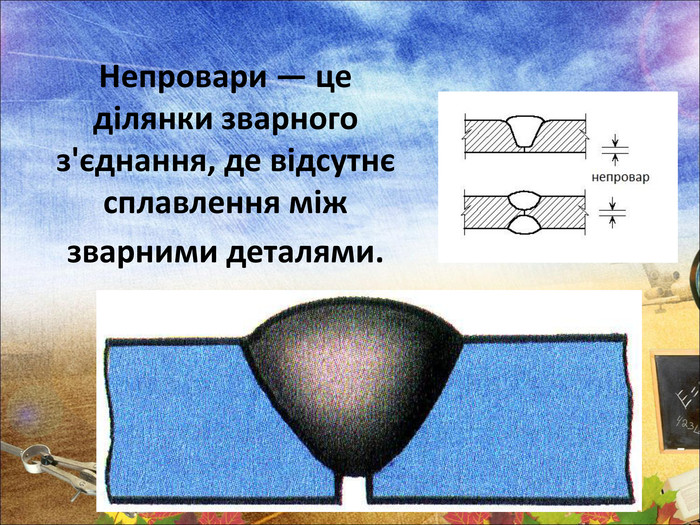



(Електроди для наплапвки металів з підвищиною зносостійкістю)
(Електроди для наплапвки деталей працючих в режимі підвищеного тертя)
(Електроди для наплавки чавуну та його сплавів)
(Електроди для наплавки алюмінію та його сплавів)
Комментариев нет:
Отправить комментарий